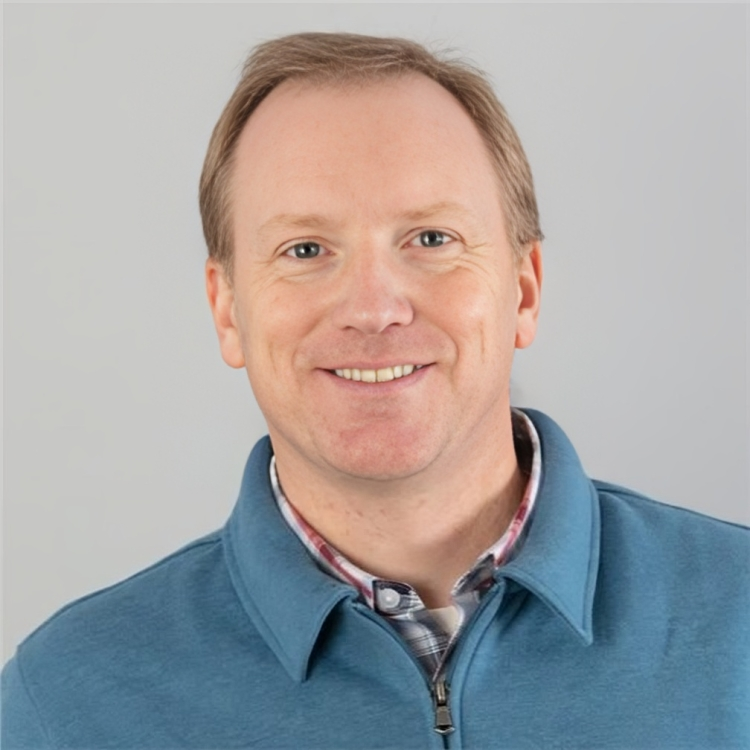
By Ken Devlin – Director, Portfolio Marketing
Few things within the four walls of a collision repair shop are as critical as your process.
Standardized and repeatable steps are the key to hitting the ever-elusive yet forever-important promise date. Sometimes it feels like your customer has that date in mind from the moment the accident happened. They ask, "When is my car going to be done?" before you've even seen the vehicle, written an estimate or built a repair plan.
Committing to a date is a challenge because what could possibly go wrong to cause a missed promise date besides anything and everything? So how do you keep your commit dates on track, while still planning for the unknown? Process.
Avoiding Surprises: Pre-Repair Scans
One of the best ways to stay on track is to make sure every vehicle is properly scanned - especially pre-scanned - and that there's a process in place to ensure it gets done. It's valuable to have the scan results prior to the start of repairs as opposed to being surprised after parts are already ordered or even worse, in the detail bay at the end of a repair.
Performing these scans 100% of the time isn't just a good idea – it's essential to helping you meet your promise dates and get customers back on the road!
Ideas on HOW to make sure these pre-scans happen are as varied as opinions on how many hours are needed to repair a dent. The important thing is to have a process in place and commit to it. It can’t just be a "some of the time" or even a "most of the time" process… it should happen ALL of the time.
Benefits of Pre-Repair Scans
- Consistency: Following the same steps every time for every vehicle regardless of the extent of damage ensures that a pre-scan gets done each and every time.
- Consistency: When committing to a process that demands that every car receives a pre-scan, it's easier to catch the ones that don't.
- Consistency: Having a process in place that is followed every time relieves employees of having to "remember not to forget." It is just part of the process, like taking the keys or signing an authorization to repair.
Yes, I used the same word to describe three different benefits; make no mistake about it, while all scan types (pre-repair, in-process and post-repair) are critical, as are calibrations, skipping a pre-repair scan can mask deeper issues, putting you behind the 8-ball to hit that all-important promise date.
Looking for tips? Watch Run My Business on YouTube.
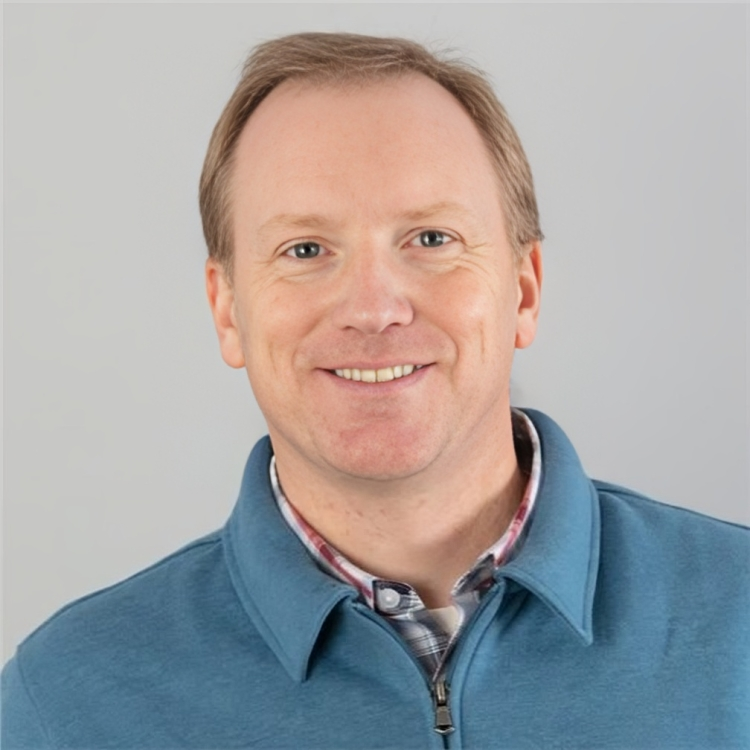
By Ken Devlin – Director, Portfolio Marketing
Few things within the four walls of a collision repair shop are as critical as your process.
Standardized and repeatable steps are the key to hitting the ever-elusive yet forever-important promise date. Sometimes it feels like your customer has that date in mind from the moment the accident happened. They ask, "When is my car going to be done?" before you've even seen the vehicle, written an estimate or built a repair plan.
Committing to a date is a challenge because what could possibly go wrong to cause a missed promise date besides anything and everything? So how do you keep your commit dates on track, while still planning for the unknown? Process.
Avoiding Surprises: Pre-Repair Scans
One of the best ways to stay on track is to make sure every vehicle is properly scanned - especially pre-scanned - and that there's a process in place to ensure it gets done. It's valuable to have the scan results prior to the start of repairs as opposed to being surprised after parts are already ordered or even worse, in the detail bay at the end of a repair.
Performing these scans 100% of the time isn't just a good idea – it's essential to helping you meet your promise dates and get customers back on the road!
Ideas on HOW to make sure these pre-scans happen are as varied as opinions on how many hours are needed to repair a dent. The important thing is to have a process in place and commit to it. It can’t just be a "some of the time" or even a "most of the time" process… it should happen ALL of the time.
Benefits of Pre-Repair Scans
- Consistency: Following the same steps every time for every vehicle regardless of the extent of damage ensures that a pre-scan gets done each and every time.
- Consistency: When committing to a process that demands that every car receives a pre-scan, it's easier to catch the ones that don't.
- Consistency: Having a process in place that is followed every time relieves employees of having to "remember not to forget." It is just part of the process, like taking the keys or signing an authorization to repair.
Yes, I used the same word to describe three different benefits; make no mistake about it, while all scan types (pre-repair, in-process and post-repair) are critical, as are calibrations, skipping a pre-repair scan can mask deeper issues, putting you behind the 8-ball to hit that all-important promise date.
Looking for tips? Watch Run My Business on YouTube.